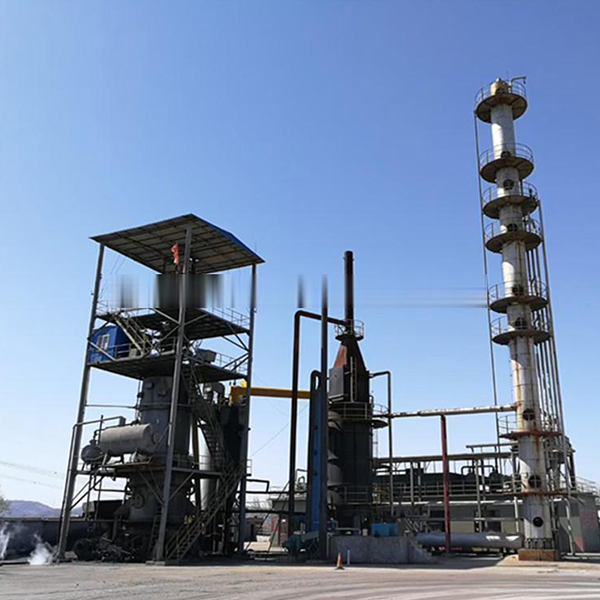
This project will adopt new improved atmospheric and vacuum process. On the basis of the original classic normal pressure reduction process, this scheme aims at the requirements of the products suitable for the separation of gasoline, diesel, heavy diesel and basic oil and gas image cracking to produce diesel oil. The process of making diesel oil by oil is simulated and calculated, and the equipment of heat exchanger and inner part of tower is selected and hydraulically calculated.
Design requirements:
The production of cracked diesel oil by this process requires that the oil yield of the product reach more than 80%(1% of the customer's raw water), and the fractionation range of diesel oil reaches the national standard distillation range after fractionation.
This project will adopt new improved atmospheric and vacuum process. On the basis of the original classic normal pressure reduction process, this scheme aims at the requirements of the products suitable for the separation of gasoline, diesel, heavy diesel and basic oil and gas image cracking to produce diesel oil. The process of making diesel oil by oil is simulated and calculated, and the equipment of heat exchanger and inner part of tower is selected and hydraulically calculated.
1. design requirements:
The production of cracked diesel oil by this process requires that the oil yield of the product reach more than 80%(1% of the customer's raw water), and the fractionation range of diesel oil reaches the national standard distillation range after fractionation.
2. process description:
Crude oil after preliminary treatment, remove impurities and some water, pump into the dehydrator, heating, heating. After heating, the moisture and a small amount of light components are removed. The material pump body in the kettle is transported to the heater and continues to heat up. With the increase of temperature, the oil and gas enter the initial distillation tower and separate the gasoline components. The top of the tower is gasoline component, after condensation, recovery. After the bottom component continues to be heated, it enters the atmospheric pressure tower, the top of the tower is light diesel oil, and the measuring line is diesel oil component. After cooling, it is sent to the storage tank. After reheating the bottom material of the atmospheric pressure tower, it enters the decompression tower. The top of the decompression tower is light component base oil, and the measuring line part of the tower is base oil. Can be reconciled and stored. The residue enters the residue tank.
3. Process Design Advantages
Accurate process simulation calculation provides a good guarantee for the separation efficiency and optimization design of the whole process;
With the optimization of heat transfer network, the energy consumption of the system is low, and the heat required for the heating of raw materials is provided by the heat transfer of the product after the normal start of work. Rich thermodynamic data and many years of laboratory experimental data accumulation, such as vapor-liquid equilibrium data, material corrosion mechanism;
The use of the inner parts of the high efficiency tower provides a guarantee for the separation efficiency; for example, according to the viscosity of the material, the packing with large flux and strong plugging resistance is used under the feed port. High separation efficiency packing is used to ensure the smell, color and other rational requirements of the product.
The control of pressure and temperature of each tower ensures the quality and recovery of the product;
Design and driving experience of multiple separation engineering experiences (services such as driving guidance and training);